
Solution for Accelerating and Increasing Efficiency in Injection Molding Production at Shangfa Factory
Industry Challenges and Solutions
High-speed part removal is a critical factor in improving production efficiency in the injection molding industry. However, traditional manipulator control systems often struggle to balance positioning accuracy and stability during high-speed operations, leading to limited productivity, fluctuating product quality, and potential safety risks. Huacheng has developed the HC and QC series control systems specifically designed for high-speed removal scenarios, helping enterprises overcome these bottlenecks.

Ultra-Fast Response and Precision Control
Leveraging a dual-core DSP+FPGA architecture, the system achieves a rapid 62.5μs response time and 0.01mm motion control accuracy, ensuring precise positioning of injection-molded parts during high-speed operations. In the case of Shangfa Factory, this system reduced the single-cycle part removal time to 0.8 seconds on the mobile phone case injection line, boosting productivity by 30% compared to traditional equipment.

Flexible Expansion and Stable Compatibility
The system supports 1-6 axis multi-joint movement and is equipped with a 500KHz high-speed pulse interface, compatible with leading servo drives in the market. By adding an IO expansion board, Shangfa Factory seamlessly integrated injection molding machines, manipulators, and automated assembly lines, reducing manual intervention and operational risks.
Equipment Configuration and Scenario Adaptation
Shangfa Factory adopted the Huacheng HC series 6-axis control system with customized grippers, tailored to the complex requirements of their automotive bumper injection line. The system uses trajectory optimization algorithms to plan 3D curved part removal paths, avoiding collisions with molds during high-speed operations.
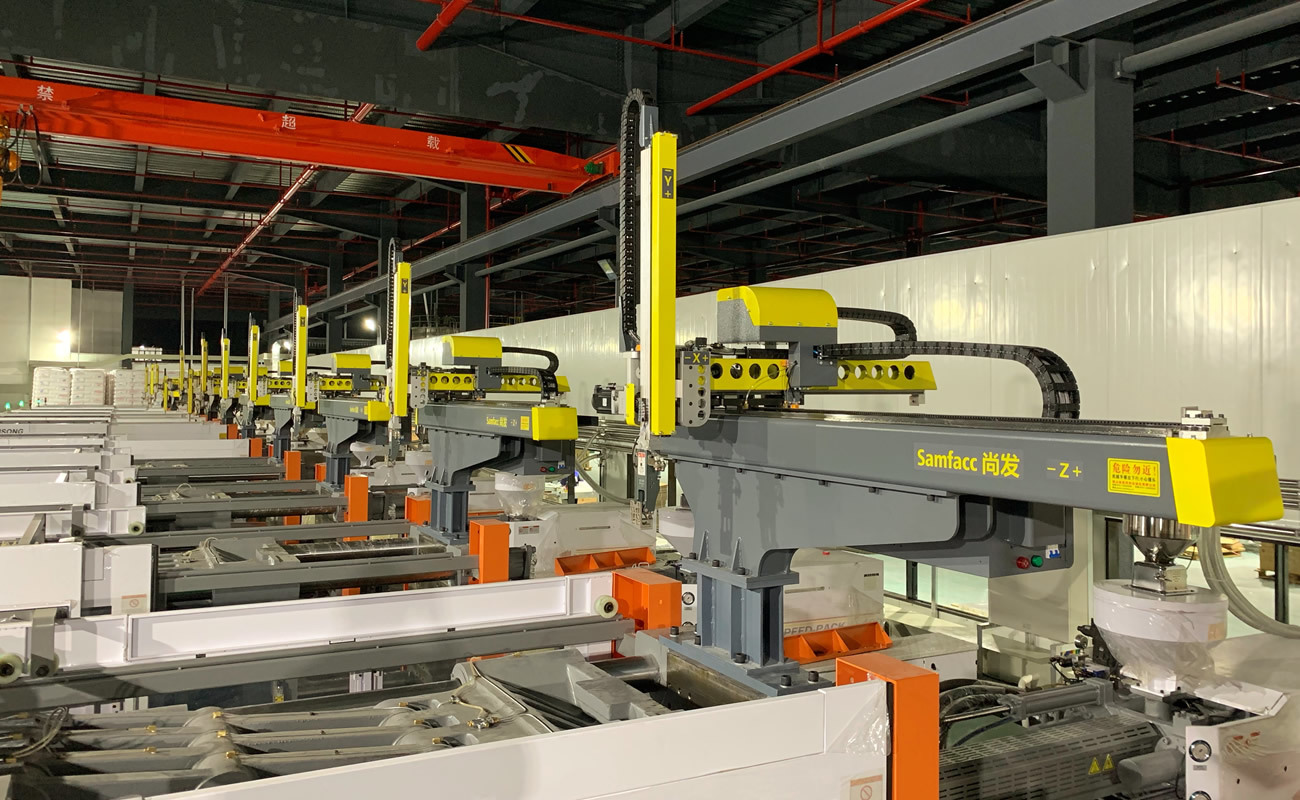
Operational Results
Cycle Time: Reduced from 12 seconds/part to 8.5 seconds/part, increasing annual capacity by ~35%.
Yield Rate: Defect rate due to positioning errors decreased from 1.2% to 0.3%.
Energy Savings: Annual power consumption reduced by ~8,000 kWh per unit through dynamic torque control.
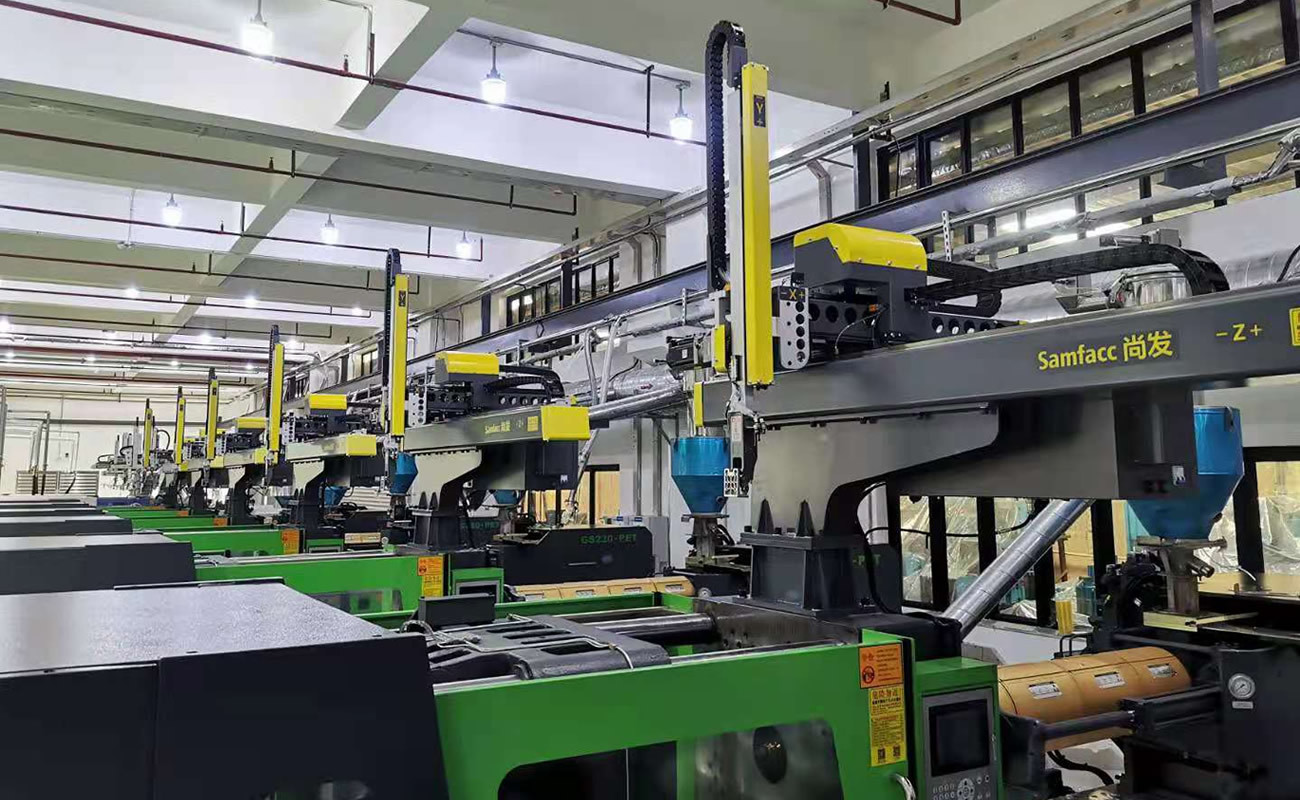
Safety and Maintenance Enhancements
The system incorporates multiple safety features, including collision detection, emergency stop, and overload protection. Feedback from Shangfa operators reported a 60% year-on-year reduction in equipment failure rates and significant maintenance cost savings.
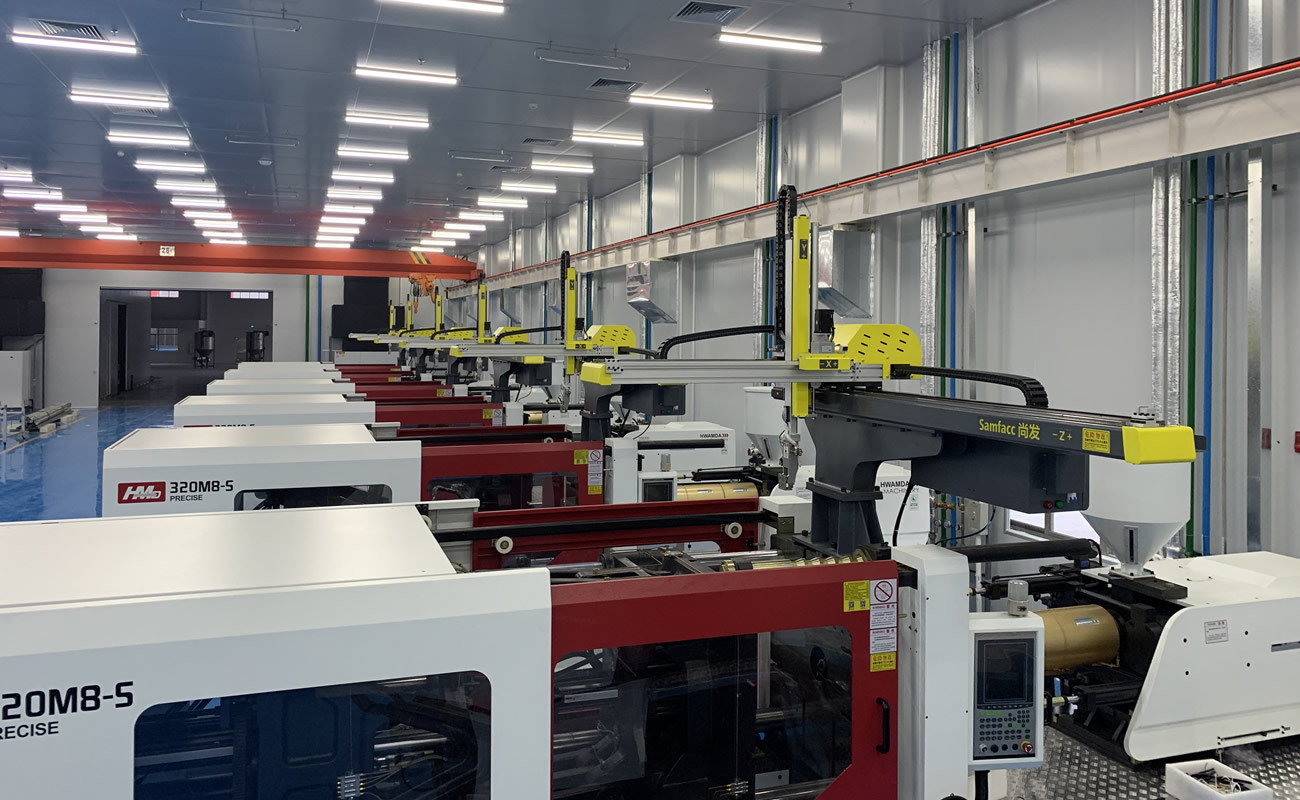
Huacheng’s injection molding manipulator control system, through technological innovation and scenario-specific adaptation, has enabled Shangfa Factory to achieve:

Efficiency Revolution
Unlocking the full potential of injection molding machines

Quality Assurance
Reducing waste through millimeter-level precision

Intelligent Upgrade
End-to-end automation minimizing manual dependency
Visual Case Demonstration





Recommed Products
Contact Huacheng’s technical team today for your customized high-speed part removal solution!
Refer a Friend
Both Get 3-10% Off hare via Form
Stay in the Know!
From time to time we will email you with updates, new products, and the best of the automation industry. We promise not to spam you.
Copyright © 2025 Shenzhen Huacheng Industrial Control Co., Ltd. | All rights reserved